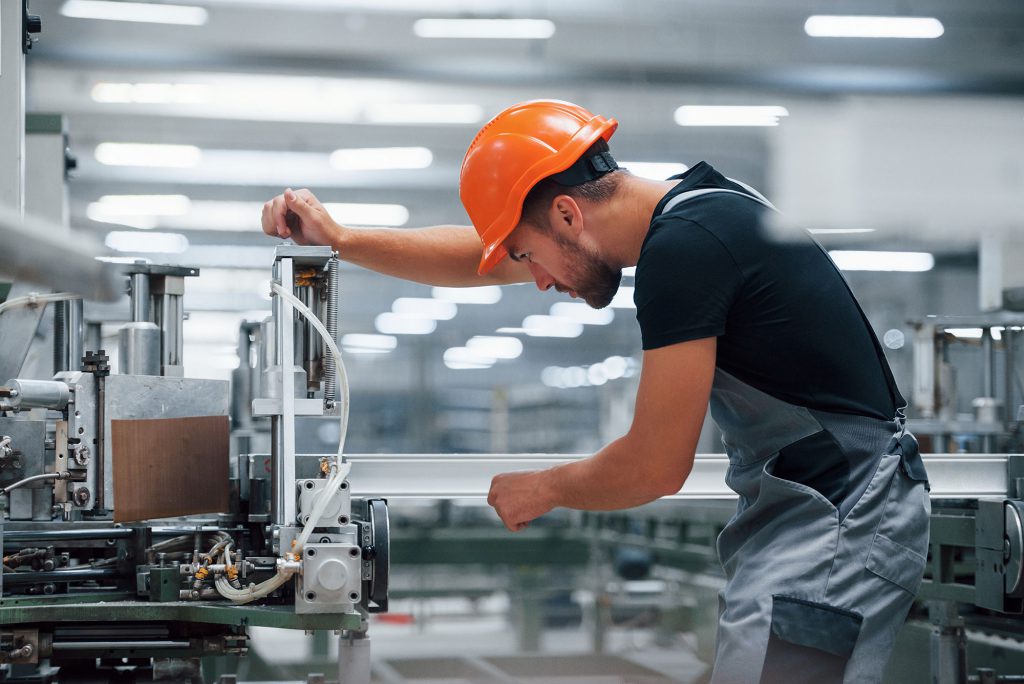
At Ahearn & Soper Inc., we understand that your label applicator is a critical piece of equipment in your production process. Proper maintenance isn’t just about preventing breakdowns—it’s about ensuring consistent quality, maximizing efficiency, and protecting your investment. This comprehensive guide will walk you through essential maintenance practices that will keep your label applicator running smoothly for years to come.
Daily Maintenance Checklist
1. Clean Thoroughly and Regularly
Every day, take a few minutes to clean your label applicator:
• Wipe down external surfaces with a soft, lint-free cloth
• Remove any adhesive residue or paper fragments
• Use compressed air to blow out dust from hard-to-reach areas
• Inspect rollers and applicator heads for buildup
2. Lubrication is Key
Regular lubrication prevents friction and wear:
• Apply manufacturer-recommended lubricants to moving parts
• Focus on pivot points, rollers, and mechanical components
• Use light machine oil sparingly and precisely
• Avoid over-lubrication, which can attract dust and debris
Weekly Maintenance Procedures
1. Comprehensive Inspection
Conduct a thorough weekly examination:
• Check all electrical connections for signs of wear
• Inspect belts and tensioners for proper alignment
• Verify sensor functionality
• Look for any unusual wear patterns on components
2. Calibration Check
Ensure your label applicator maintains precision:
• Test label placement accuracy
• Adjust sensors and alignment mechanisms
• Verify label feed and application speed
• Recalibrate according to manufacturer specifications
Monthly Deep Maintenance
1. Component Assessment
Perform a more detailed monthly evaluation:
• Examine wear on cutting mechanisms
• Check and replace worn rollers
• Inspect electrical components for potential issues
• Verify software and firmware are up to date
2. Professional Diagnostic Review
Consider scheduling periodic professional maintenance:
• Have a certified technician perform a comprehensive diagnostic
• Address potential issues before they become major problems
• Update calibration and alignment settings
• Receive professional recommendations for optimal performance
Common Warning Signs to Watch For
Be alert to these potential maintenance red flags:
• Inconsistent label placement
• Unusual noises during operation
• Reduced application speed
• Frequent paper jams
• Visible wear on applicator components
Choosing the Right Maintenance Supplies
Invest in quality maintenance materials:
• Use manufacturer-recommended cleaning solutions
• Purchase genuine replacement parts
• Select appropriate lubricants designed for precision equipment
• Keep a maintenance log to track repairs and interventions
Training and Documentation
Effective maintenance requires knowledge:
• Train all operators on proper equipment handling
• Create a standard maintenance protocol
• Keep the manufacturer’s manual easily accessible
• Document all maintenance activities
Cost of Neglect vs. Cost of Maintenance
Consider the financial perspective:
• Routine maintenance costs a fraction of major repairs
• Preventative care extends equipment lifespan
• Reduces unexpected downtime
• Maintains consistent production quality
Conclusion
Your label applicator is more than just a machine—it’s a critical investment in your production capabilities. By implementing these maintenance strategies, you’ll not only extend its operational life but also ensure consistent, high-quality performance.
At Ahearn & Soper Inc., we’re committed to helping you maximize your equipment’s potential. Remember, proactive maintenance is always more cost-effective than reactive repairs.
For personalized maintenance advice or to schedule a professional equipment review, contact our expert technical support team.